What is Heat Treatment?
After aluminum cools in the casting process, it is engrained with specific “as cast” strength characteristics. Most applications require aluminum castings to have different mechanical properties, metallurgical structure or tensile strength that an aluminum casting will not have “as cast”. Heat treatment is used to strengthen and improve the structure of cast aluminum parts.
Solutions for Heat Treat at TPi Arcade
TPi has the capability to perform T51, T6 and T7/T71 tempers. The heat treatment systems are on premise here at the foundry and annually calibrated by Honeywell as per our AS9100 quality system. Time and temperature charts are recorded for all heat treatments and filed electronically to provide traceability. Our Quality Lab also includes a tensile bar test machine and Brinell Harness test to verify heat treatment results.
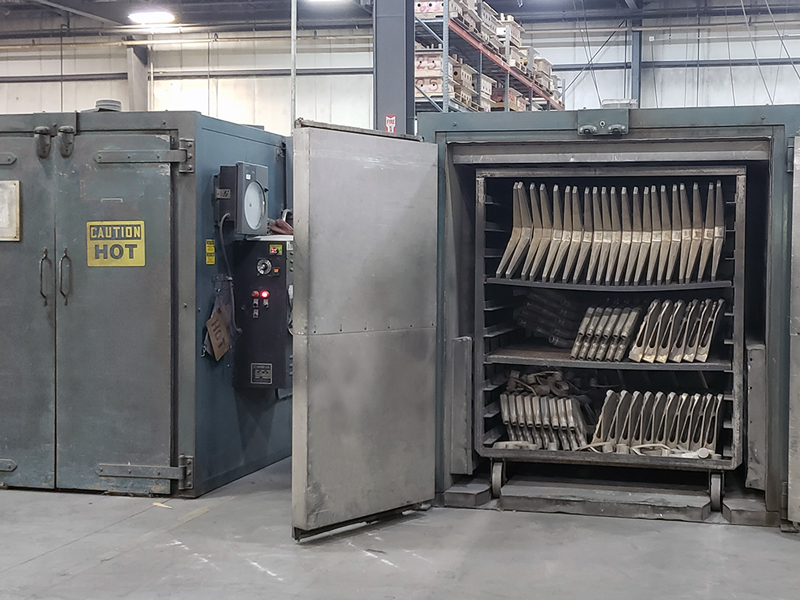
T51 Temper
T51 heat treatment process bakes the casting at a low-temperature to artificial age it. The temperature range is between 440˚F (227°C). The casting is heated in the oven for 3-5 hours and then allowed to cool naturally. The low temperature stabilizes the shape of the castings and reduces stresses in the aluminum.
T51 parts do not hold the same strength properties as T6. However, the T5 process’ naturally slower cooling method reduces part distortion and warping.
T51 temper is the most commonly requested heat treatment at TPi. The mechanical properties are 23 KSI (160 MPA) Ultimate Tensile Strength, 16 KSI (110 MPA) Yield Strength and 45-75 Brinell Hardness. It is typically utilized in non-structural applications such as instrumentation, medical, power electronics, semi-conductor and robotics and many others
Benefits of T51:
- Less distortion than T6
- Stress relief to improve machining of casting
- Increased mechanical properties compared to as cast
T6 Temper
A T6 heat treatment is three steps. During the first step, the casting is heated at a very high temperature, 1,000°F (538⁰C) for 12 hours. The next step is quenching. The casting is lowered into a liquid solution bath resulting in rapid cooling. The solution bath is usually water or glycol at a temperature 150-214°F (66-100°C). After quench, the castings are aged in a furnace. They are heated to 310°F (154°C) for 3-5 hours and then allowed to cool naturally..
The quenching process often causes distortion and stresses in parts. This is because of the extreme temperature differentials between the heated casting and the quench cooling solution. A straightening process is performed after quench and prior to age to ensure parts are to print. This quenching is necessary to achieve the higher mechanical properties of T6. The mechanical properties are 34 KSI (235 MPA) Ultimate Tensile Strength, 24 KSI (165 MPA) Yield Strength, 3.5% Elongation and 70-105 Brinell Hardness.
T6 temper is the second most commonly requested heat treatment at TPi. It is typically utilized in structural applications such as automotive, robotics, aerospace, defense and marine among others.
Benefits of T6:
- Higher mechanical properties
- Less deformation under heavy loads
- Harder aluminum
T7 & T71 Temper
This is the least common heat treatment performed at TPI. T7/T71 heat treatment process is generally the same as T6 except the temperature of the aging after the quench. Like in T6, T7 and T71 castings are heated at 1,000°F (538⁰C) for 12 hours and quenched at is aged at 150-214°F (66-100°C). For T7, castings are aged at 440˚F (227˚C) for 7-9 hrs. T71 is aged at 475˚F (204˚C) for 3-6 hrs.
The mechanical properties for T7 are 31 KSI (215 MPA) Ultimate Tensile Strength, 29 KSI (200 MPA) Yield Strength, 3% Elongation and 60-90 Brinell Hardness.
The mechanical properties for T71 are 25 KSI (170 MPA) Ultimate Tensile Strength, 18 KSI (125 MPA) Yield Strength, 3.5% Elongation and 45-75 Brinell Hardness.
T7 & T71 Temperhave the same benefits as T6 but have different mechanical properties.
