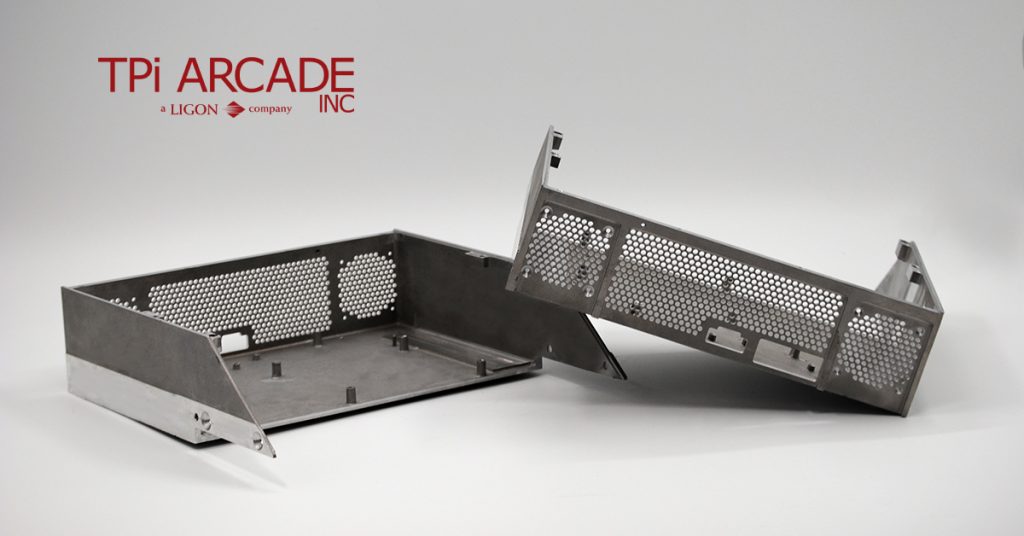
TPi Arcade has substantial experience in converting aluminum billet parts to V-Process sand cast parts. A V-Process sand casting conversion offers minimal compromise on finish or shape.
Initially, companies often chose billet machining for its net shape precision, minimal tooling dollars and short lead times. It can be a cost effective option at lower quantities. If production increases, piece prices often plateau making the part too expensive to be very profitable. So what alternatives are there when billet machining becomes uneconomical?
Sand casting can be a good alternative but typical sand casting is not always feasible. Typical sand casting requires additives or chemicals. They bind the sand together in order to hold the shape of the pattern. This causes a rougher surface finish (250 – 500 RMS). Finally, sand casting requires the addition of 1° – 5° draft stock to the pattern. This further reducing accuracy, decreasing real estate for mating components and adding unnecessary weight.
V-Process sand casting holds the sand in shape under vacuum instead of utilizing additives. This vacuum process produces a smoother surface finishes (125 RMS), 0° draft and thinner walls (.125” min). Thus producing a near net shape comparable billet machining.
Converting to V-Process sand casting from billet machining can reduce cost. Read more in this article on Casting Source about how TPi was able to cut their piece price by 80%.
Click here to read: “Vacuum Process Cuts Costs By 80% Over Machined Billet”